Production Supervisor - Point Tupper, Canada - Cabot Manufacturing ULC
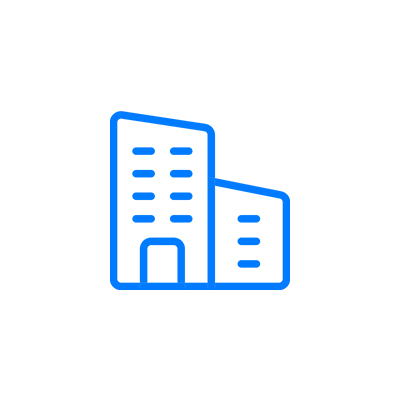
Cabot Manufacturing ULC
Point Tupper, Canada
Verified Company
3 weeks ago
Description
Job Overview:
We are looking for an individual who will strive to make a difference and want to join an engaged dynamic team.
As a dynamic Production Supervisor your job will include scheduling personnel to ensure productive ways to meet or exceed established production targets.
Your objective is to work with your team to minimize equipment downtime, improve operations reliability and maximize productivity. Furthermore, support the reduction of waste and unnecessary lost time to facilitate the overall reduction of operating costs.Your technical production expertise, leadership and guidance will be an asset to the operations and maintenance team as they work to improve overall production reliability efficiency.
Key Responsibilities:
- Conducts daily safety toolbox meetings, with emphasis placed on Safety compliance.
- Maintaining a safe and clean work environment by educating and directing personnel to ensure safety compliance and housekeeping.
- Maintaining compliance with Plant established Policies and Procedures.
- Providing an example of safety to the direct reports by adhering to safety policies and holding direct reports to the same standard.
- Prioritize first pass quality through operator ownership of quality and limiting run time during a quality issue to reduce the number of rejects and/or holds.
- Monitoring the quality of the product. Immediately addressing and reporting any issues to the Operators, Quality Techs, and Quality Manager.
- Ensuring all operators have performed their preplanning for production and check lists performed at each work station at startup, during production and shutdown.
- Effectively communicating to the crew, the product schedule, product speed and any associated changes and their associated run rates, productivity, and attainment targets.
- Tasking the crew with alternative duties during breakdown or material shortages to maximize the efficiency of labour resources. Ensuring every employee has a secondary responsibility.
- Collaborating with other Departments, Safety, Maintenance, Quality and Warehouse to ensure alignment of objectives and any relevant issues.
- Organizing the crew so that all work stations and breaks covered following continuous production model.
- Providing detailed Break Down Reports to capture down time minutes per occurrence and the associated issue, if possible, the root cause.
- Coaching, and facilitating performance Management actions to employees as required.
- Ensuring compliance with Plant processes, Policies, and Standard Operating Procedures.
- Maintaining workflow by monitoring steps of the process; observing control points and equipment; monitoring personnel and resources.
- Troubleshooting problem areas when possible, involving others such as Operators and Trades.
- Establishing priorities based on the schedule and as added information becomes available.
- Monitoring progress of new hires taking responsibility for training effectiveness
- Production reporting to Departments via electronic distribution list and hard copies for review.
- Focus on the quality expectations and report to the Quality Manager and Team any issues, or anything that may cause a change in quality to facilitate an initiativetaking quality culture.
- Ensuring effective operation of equipment, calling for repairs, as required to prevent down time and evaluating equipment function to ensure equipment efficiency.
- Attends daily and weekly staff meetings to review Production Results and Improvement opportunities.
- Supports maintenance days with the production team performing housekeeping and soft maintenance associated duties.
- Reduce waste of raw material when and where possible following LEAN concepts.
- Submitting production results and shift report before leaving each shift.
- Other tasks as required to meet our Production objectives.
Position Requirements:
- Minimum 2 years experience Supervising Teams in a Manufacturing environment, or equivalent work experience required.
- You possess strong values related to Safety leadership and Safety programs.
- Experience and knowledge related to Quality right firsttime concept and Quality programs.
- Periodically conducts equipment inspections with trades and/or operations to evaluate the assets, including the support of root cause analysis.
- Conducts quality assurance WO data checks and produces reports based on findings.
- Strong skills in predicting trends based on historical data to ensure downtime is minimized and reliability of the equipment is optimized is considered an asset.
- Performs and/or reviews research and calculations and analyzes technical data.
- Planning, scheduling & assigning work to the appropriate employees based on priorities, required skills & resources avai