Operations Manager - Edson, Canada - NAES CANADA LTD
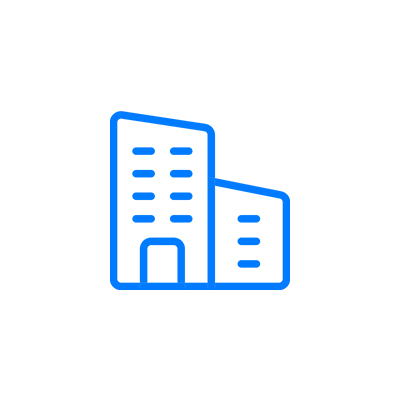
2 weeks ago
Description
Opportunity Summary
As an essential member of the leadership team, the Operations Manager is responsible for ensuring plans, processes and measures are in place to achieve safe, efficient and reliable operation and maintenance of the facility; to maximize operational effectiveness and ensure compliance with regulatory standards and contractual commitments; to operate the facility in accordance with equipment manufacturer instructions to achieve optimum performance and profitability of the facility and provide support to maintenance and engineering teams.
The Operations Manager assumes the role of Chief Operating Engineer as defined in the Power Engineering regulations and provides leadership and mentoring for the operations team.
Primary Functions
- Takes ownership and leads in the communications of NAES' Mission and Vision to the Operations staff
- Responsible for ensuring that the safety management systems are in place to ensure safe work and that these systems are followed rigorously
- Responsible for ensuring that environmental monitoring and reporting systems are in place and are adequate to meet corporate and regulatory requirements
- Responsible for the identification of primary operational risks for the facility and the development of risk mitigation strategies where appropriate
- Responsible for maintaining communications and management of relationship with energy trading and ISO in regard to daily and planned plant capacity and any limitations
- Responsible for ensuring plant operating capabilities are tracked
- Responsible for updating operational component of Operations & Maintenance (O&M) Plan based on sound asset management planning
- Responsible for meeting the performance factor targets as prescribed in the O&M plan and ensuring all staff and procedures meet quality and training levels to achieve factors
- Responsible for developing and monitoring Key Performance Indicators (KPIs) for plant and educating plant staff in the understanding of the measures
- Responsible for understanding the chart of accounts and ensuring that transactions are booked against the appropriate cost center and account
- Responsible for management of Alberta Reliability Standards (ARS) program in compliance with requirements
- Responsible for ensuring operational and reliability information is incorporated into the major maintenance plan and ensuring that any findings or developments from major maintenance are incorporated in operating practices
- Develops departmental goals from performance goals
Accountabilities
- Accountable for ensuring that Operations personnel have all necessary skills and training needed for completion of their role and that adequate records are maintained to verify training and development is adequate
- Accountable for achieving targeted availability, reliability and starting reliability targets
- Accountable for managing all operationsrelated supplier relationships including, but not limited to, chemical, fuel, ammonia and water treatment suppliers
- Accountable for the development of generation, heat rate and performance standard budget for one to five years
- Accountable for Operations cost budget including variable operating costs (chemical and water treatment costs)
- Accountable for the collection and evaluation of Reliability Availability Maintainability (RAM) data in a consistent and accurate fashion
- Accountable for the development of the longterm operating budgets and availability forecasts based on maintenance plans
- Accountable for the development, implementation, and use of Operations Procedures required for the safe and reliable operation of equipment as well as emergency response, pressure component Quality Control (QC), environmental controls, waste management and compliance to regulations
- Accountable to ensure direct reports understand and can communicate the corporate HSE policies
Physical Requirements and Working Conditions
Physical requirements include the possibility of standing for extended periods as well as stair and ladder climbing. Protective equipment must be worn in the performance of some duties (e.g. hard hats, safety glasses, air masks, ear protection, chemical suits, hot gloves and high voltage protective equipment, etc.).
Position requires extended working hours and varied shifts with the possibility of weekend and holiday work, as required by schedules, workload and plant conditions.
All employees will participate in the Fitness for Duty Program. This program includes a post-offer physical examination and drug screening and post-employment random drug screening. There are extensive smoking restrictions in and around the facility.
Required Qualifications
A valid First Class Power Engineer certificate is a requirement along with:
- An undergraduate degree in a related field; or
- Technology Certificate in an engineering or
More jobs from NAES CANADA LTD
-
Instrumentation, Controls and Electrical
North Bay, Canada - 2 weeks ago
-
Instrumentation, Controls, and Electrical
Loyalist, Canada - 2 weeks ago